Custom Welding Fixtures: Boost Efficiency & Precision in Manufacturing
Tailor-Made Welding Fixtures to Reduce Errors, Increase Productivity, and Cut Costs
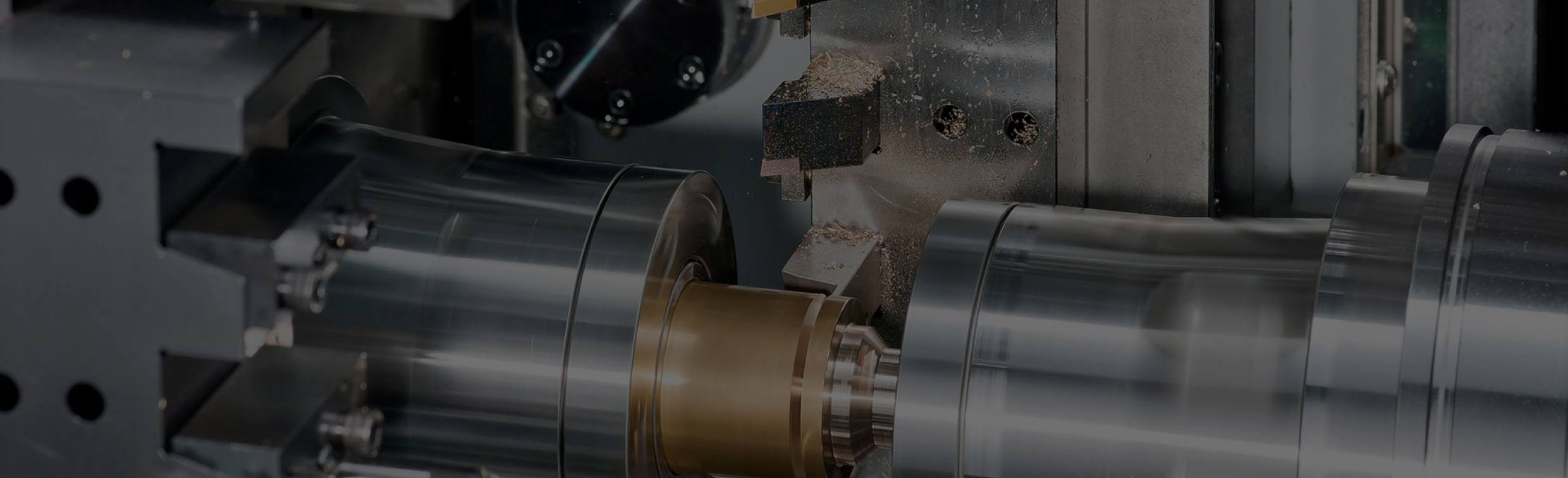
Tailor-Made Welding Fixtures to Reduce Errors, Increase Productivity, and Cut Costs
EA Engineering is an experienced manufacturer and developer of welding fixtures, specializing in their design and production. These devices receive special attention from our company due to their critically important roles. Firstly, welding fixtures allow for high precision and reliability in assembling parts before welding, significantly enhancing the quality and strength of weld joints. Secondly, these devices greatly increase the efficiency of welding processes by reducing the waiting and adjustment time. As a result, our clients not only achieve highly accurate and reliable welds but also save time and resources. Whether it is manufacturing metal structures or building vehicles, our welding fixtures consistently deliver the highest quality and performance. With our extensive experience and expertise, we are proud to offer our clients the most advanced and reliable welding solutions.
The fixtures produced by EA Engineering are remarkably versatile and capable of adapting to diverse production requirements. Our team designs devices that can be easily configured to suit the specifics of various parts, ensuring reliable and stable securing during welding operations. This results in enhanced safety and quality of assembly and welding work, as well as significantly reduces the likelihood of defects, thus speeding up production processes. Our products are also equipped with advanced automated control systems that allow us to precisely monitor all welding parameters and instantly adapt to changing work conditions in real-time. Thanks to efficient integration with robotic welding systems, we significantly boost overall productivity and minimize labor costs, making our fixtures an ideal choice for enterprises aiming to automate and optimize manufacturing processes.
EA Engineering has successfully completed numerous projects where our welding fixtures played a key role. Our innovative solutions have significantly enhanced the productivity and quality of welding at many enterprises, simplifying complex and labor-intensive processes.
If you wish to enhance the quality of your welding operations, do not hesitate to contact us for more information or a consultation. Our experienced specialists are always ready to help you design and implement a welding fixture that fully meets your requirements. Do not delay. Contact us today to discuss your needs and start working on your project.