Design and manufacturing of aggregate machines
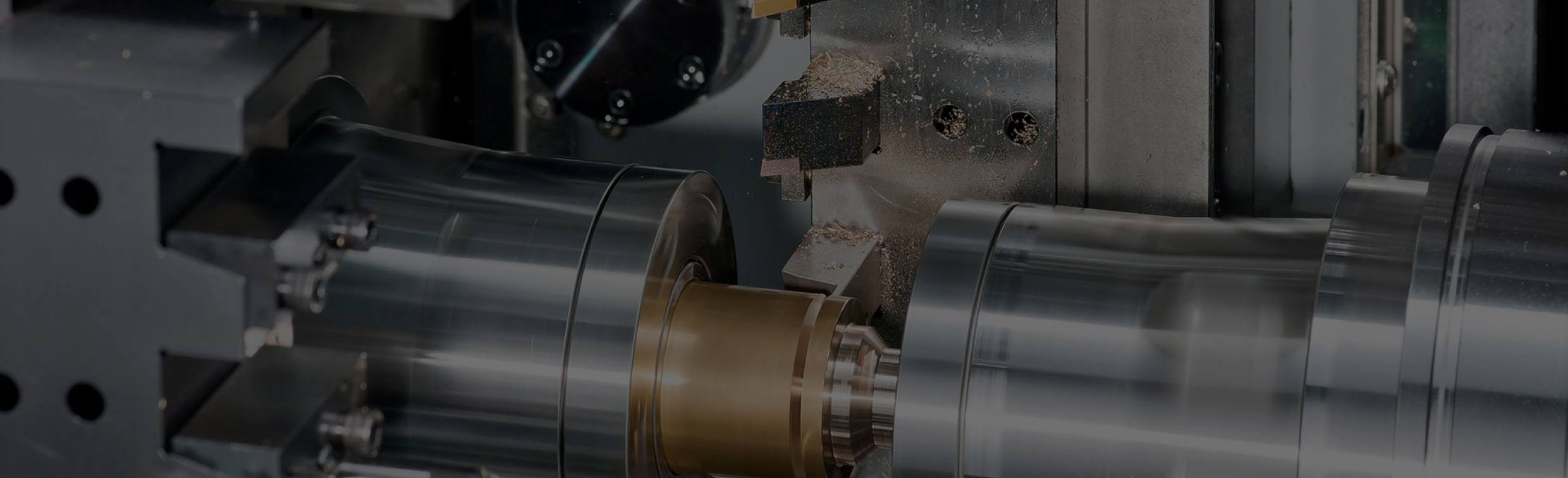
Our team at EA Engineering is an experienced manufacturer and developer of aggregate machines, specializing in their design and production. These devices receive special attention from our company as they play few exceptionally important roles. Firstly, aggregate machines allow achieving high precision and reliability in part assembly before welding, thereby significantly enhancing the quality and strength of the welds. Secondly, these devices greatly increase the efficiency of welding processes by reducing the waiting and adjustment time. As a result, our clients can achieve not only highly accurate and reliable welds but also save time and resources. Whether it's metal structures production or automotive plant, our aggregate machines are always ready to provide the highest level of quality and performance. Based on our extensive experience and expertise, we are proud to offer our Indian clients the most advanced and reliable solutions in welding.
What is an aggregate machine?
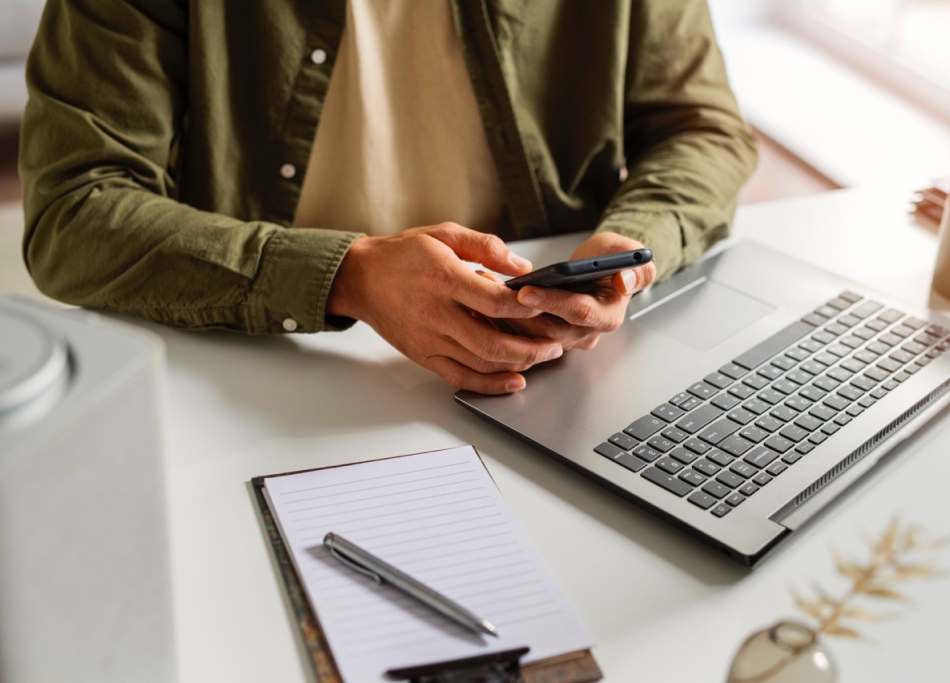
Advantages of aggregate machines from EA Engineering
The machines produced by EA Engineering are remarkably versatile and can adapt to diverse manufacturing requirements. Our team designs devices that can be easily configured to suit the specifics of different parts and provide reliable and stable attachment during welding operations. As a result, the safety and quality of assembly-welding operations are enhanced, and the likelihood of defects is significantly reduced, which greatly speeds up the manufacturing processes.
Our products are also equipped with advanced automated control systems that allow us to accurately monitor all parameters of welding operations and instantly adapt to changing working conditions in real-time. Thanks to effective integration with robotic welding systems, we greatly increase overall productivity and minimize labor costs, making our machines an ideal choice for enterprises aiming to automate and optimize manufacturing processes.
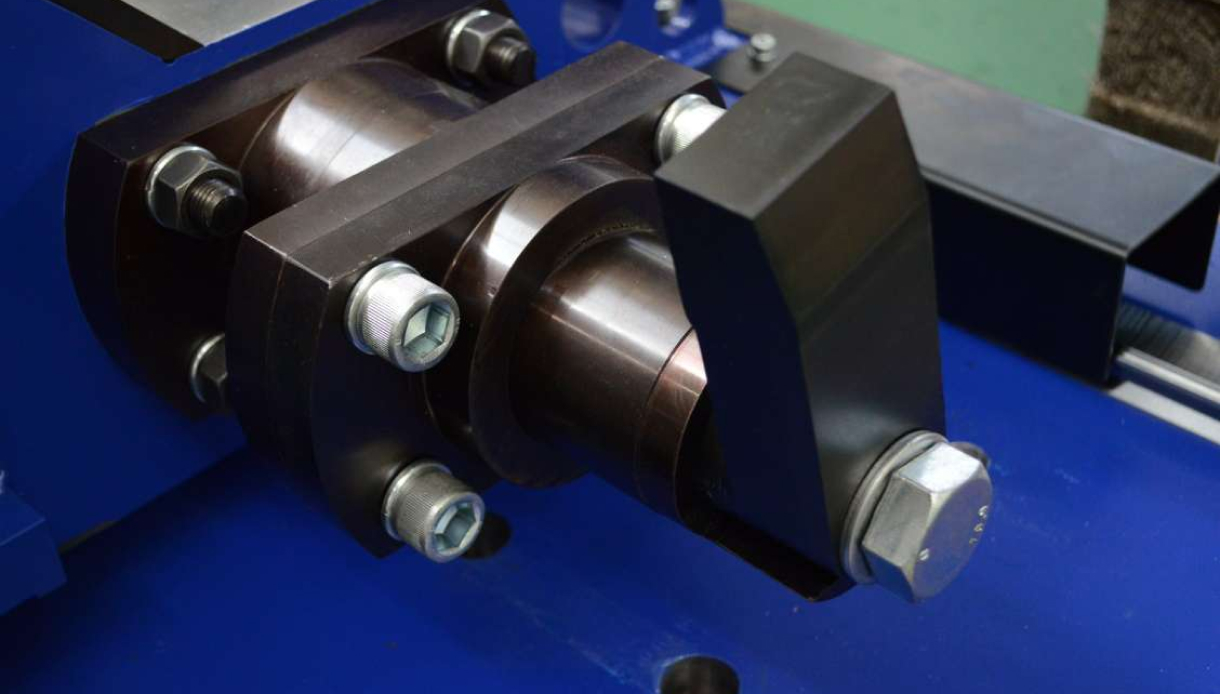
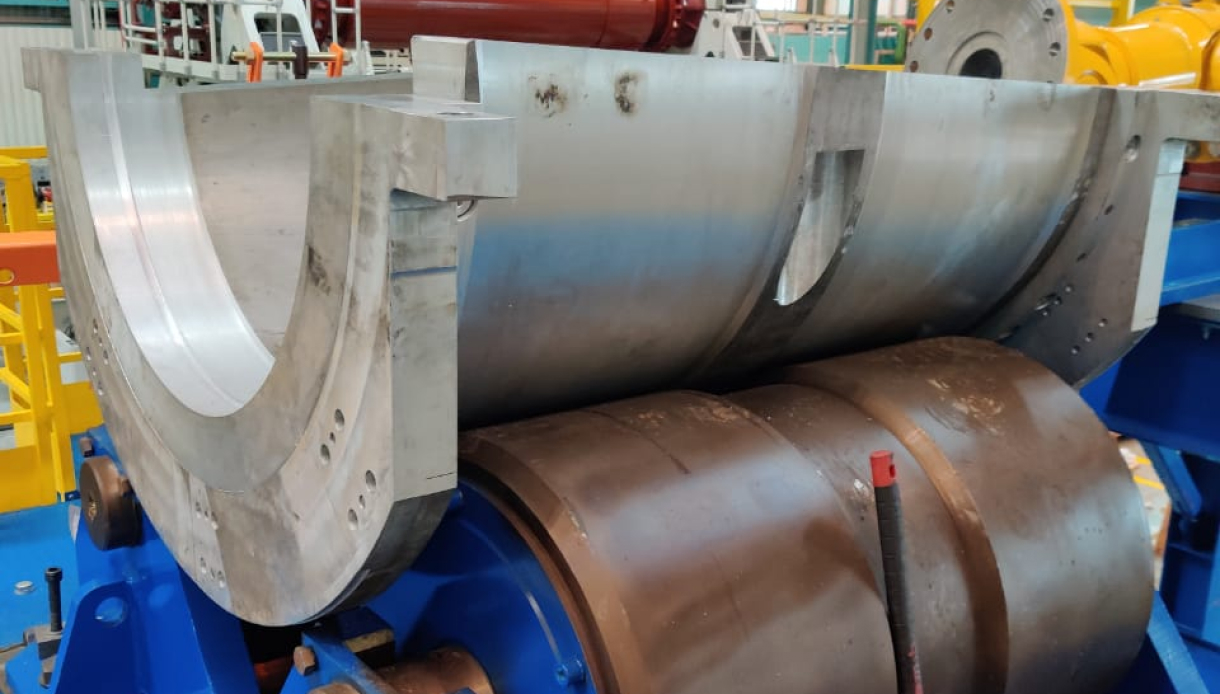
Design and manufacturing process of aggregate machines at our company
Examples of completed projects
We have successfully executed projects in the automotive, agricultural, and construction industries, showcasing the unique capabilities of our modular machine tools in action. Our clients have noted a significant increase in efficiency and a reduction in operational expenses.
Our technological capabilities
Contact us
Contact us today to discuss your manufacturing needs and how our modular machine tools cansolve your challenges.
Warranty for manufacturing modular machine tools from EA Engineering
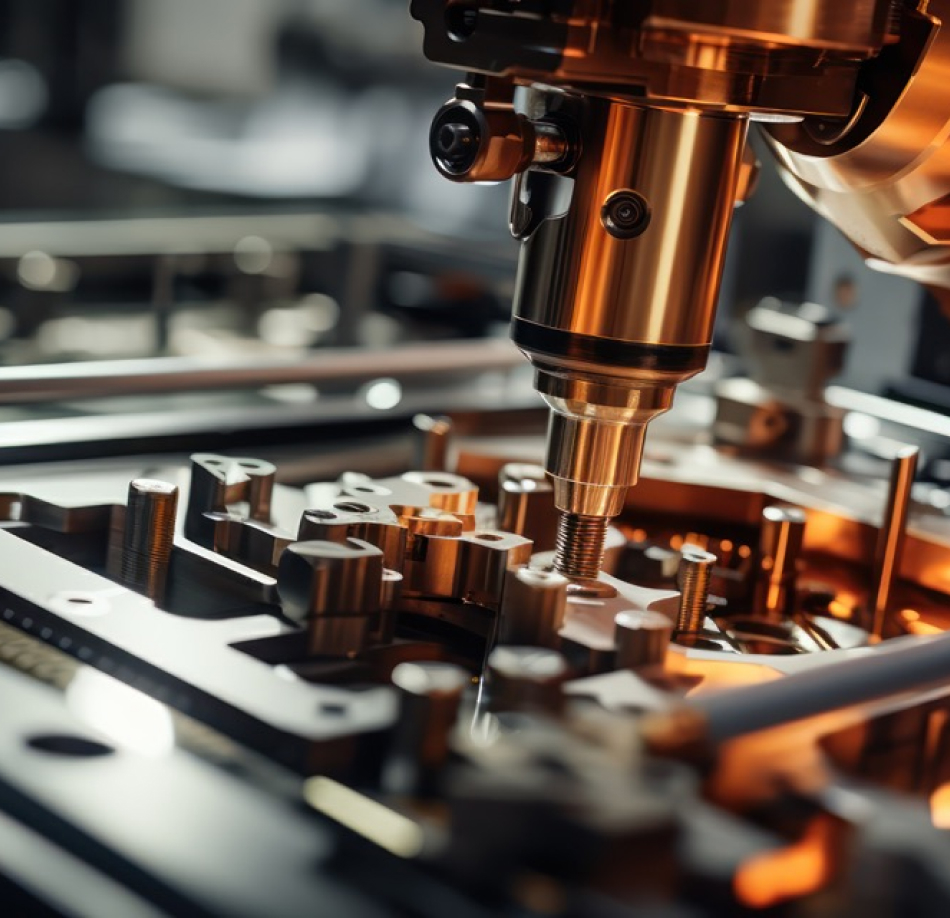
Modular machine tools: diversity and functionality
- Horizontal single-spindle. Ideal for performing single-position tasks.
- Vertical single-spindle. Ensures precision in vertical machining.
- Inclined single-spindle. Optimized for specialized angled operations.
- Multi-spindle single-position. With multiple power heads for increased productivity.
- Multi-spindle multi-position. Designed for complex machining, allowing operations from multiple sides simultaneously.
- Horizontal and vertical single-position. For efficient one-sided machining.
- Combined single-position. Combines several processes in one device.
- Multi-position machines. Ideal for sequential and complex machining of workpieces in automated flows.
Modular machine tools can operate as standalone units or as part of automated lines, facilitating the machining of stationary workpieces with multiple tools. This speeds up work processes, allowing tools to simultaneously move and process products from various sides.
Standardized components are used to develop such machines, which significantly reduces development time and simplifies manufacturing. This approach enhances adaptability to changing production tasks and allows for the creation of modular machines using a minimal number of unique parts, thereby streamlining and standardizing technological processes.
Modular machine tools can be classified based on the sizes of the workpieces they handle, allowing for three main categories. Each category is characterized by unique dimensions, weight, and design of standardized components.
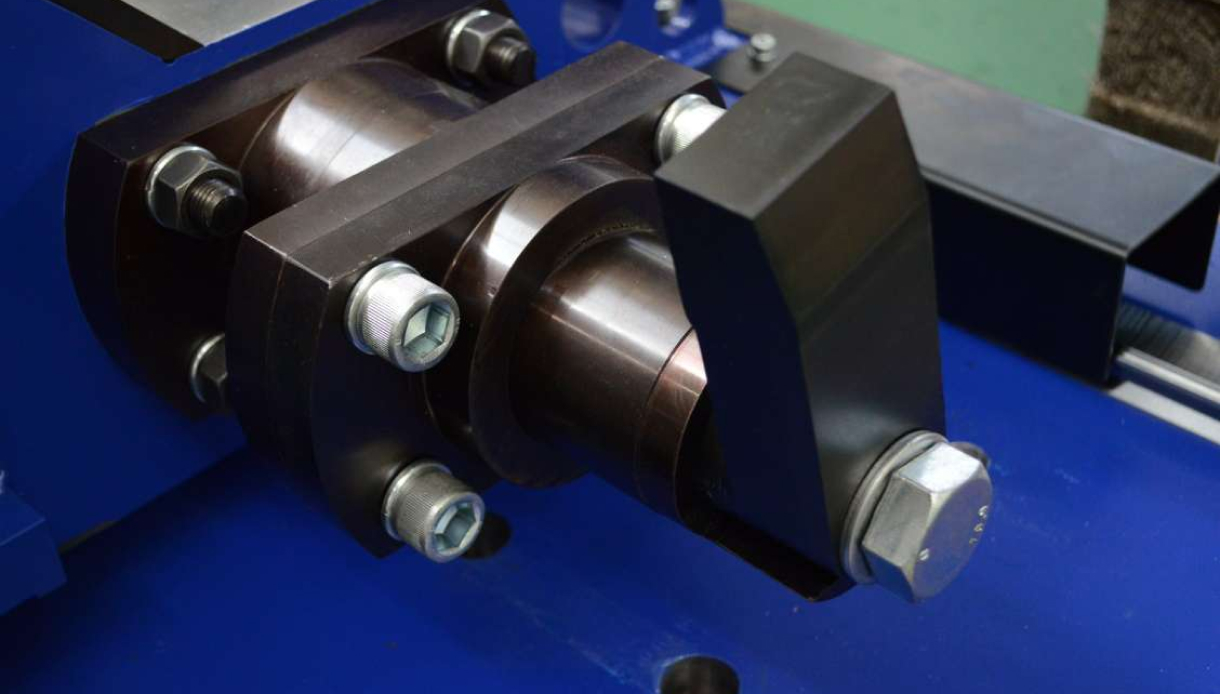
These machines are equipped with smaller spindle heads ranging from 0.18 to 0.75 kW, ideal for precise and fine work.
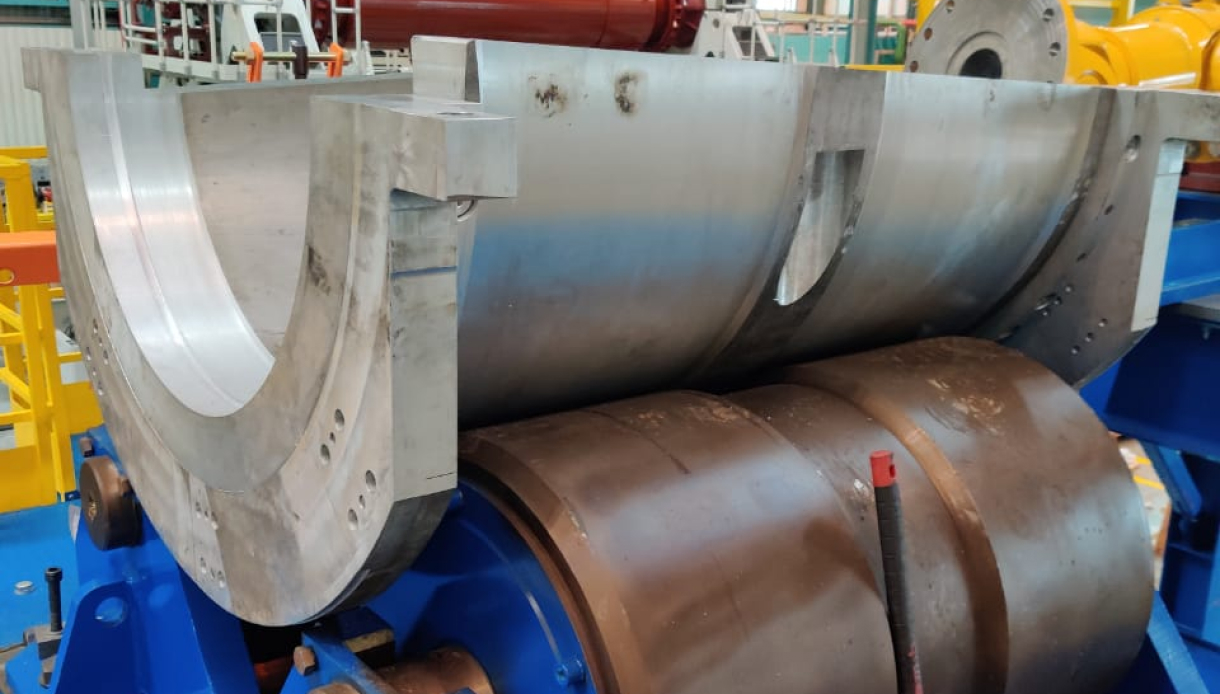
Machines in this category are fitted with cam-driven power heads providing feed power from 1.1 to 3 kW, suitable for moderately complex tasks.
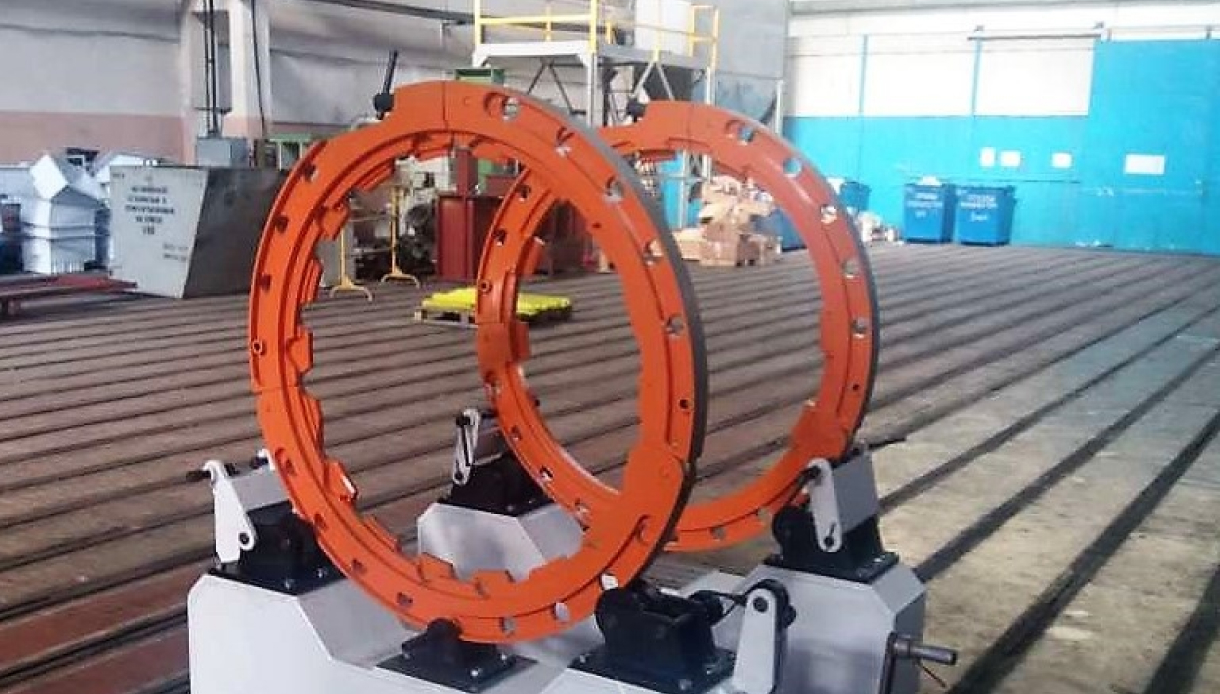
These machines include hydraulic or electromechanical tables designed to accommodate spindle units, making them ideal for processing large and heavy workpieces.
Additionally, modular machine tools can further be classified based on structural features, considering different performance requirements and processing specifications. This allows for the selection of the most suitable model for specific production needs.
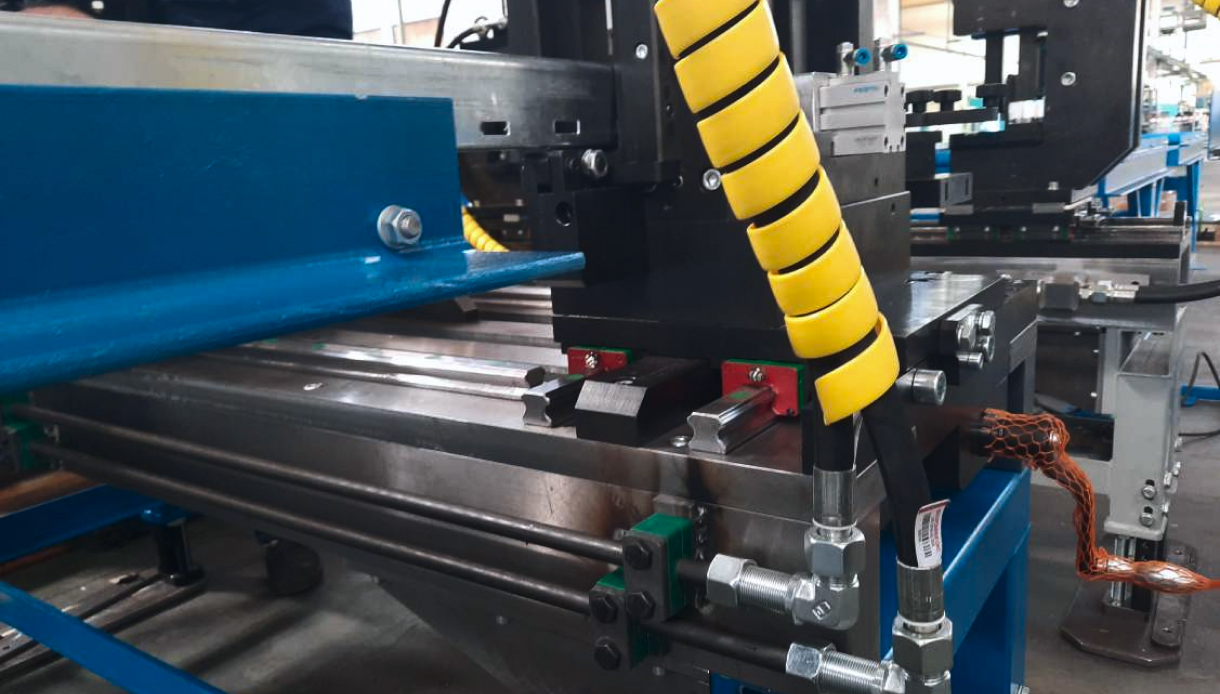
Linear type modular machine tools
Linear type modular machine tools should be noted for their leading role in the effective classification of machine equipment. These mechanisms are ideally suited for performing drilling, milling, and threading operations, thanks to their special design, which does not involve a fixed base. Modular machine tools consist of a frame equipped with guides, an electric motor, and a tool holder, enabling the workpiece to be secured in a device designed for this purpose.
In modern industry, the flexibility of equipment combined with flawless performance is especially valued. CNC modular machine tools excellently meet these demands, standing out as a separate group due to their adaptability and smooth operation.

Contact us
We guarantee the high accuracy and performance of our equipment and a reduction in the time required for design and manufacturing. Our main goal is to help you accelerate processes and reduce production costs while ensuring ease of maintenance and adaptability to process changes.
Do not miss the opportunity to enhance your business's profitability. Submit a request for the design and manufacturing of modular machine tools at EA Engineering today and confidently take each step in your production journey!